News Story – Incident / Accident / Prosecution
Waste company director sentenced over failure to comply with HSE notices
A director of a Kent waste company has been disqualified from being a director for five years for his role in its failure to comply with two Improvement Notices served by the Health and Safety Executive (HSE).
David Richard Barker, director of BSP (Knockholt) Limited, was also sentenced to two 12-month community sentences, to run concurrently, to include 12 months of supervision and 80 hours of unpaid work.
An HSE inspection in August 2020 found that employees manually sorting through waste in the company’s yard near Orpington were at risk of being struck by heavy machinery, and that there were inadequate rest facilities for them to use during break times.
Two Improvement Notices were served on the company in September 2020, and a date for compliance in October 2020 was set. Improvement Notices can be served on companies or individuals when HSE inspectors are of the opinion that they are breaching health and safety regulations. They are given a specified amount of time to improve their practices to comply with their legal duties.
However, a further site inspection in February 2021 found that the company had not complied with either notice. The company went into liquidation in 2022 but it was prosecuted and fined £150,000 in March 2023.
Mr Barker, one of the company’s directors and its main controlling party, told HSE during that he had appealed against the Improvement Notices but did not provide any evidence. In an email sent to an inspector, he also suggested that the only way to resolve differences of opinion between HSE and the company about the safety of its working practices would be for HSE to bring a prosecution against it.
Although Mr Barker was not present at the site during either inspection, HSE inspectors were told to direct all enquiries regarding health and safety to him.
At Croydon Crown Court, David Richard Barker, of Crockham Hill, Edenbridge, Kent, was previously found guilty after trial of breaching Sections 37(1) and 33(1)(g) of the Health and Safety at Work etc Act 1974, in that the offences of contravening the requirements imposed by the Improvement Notices were committed with his “consent, connivance or were attributable to his neglect”, such that he, in addition to BSP (Knockholt) Limited, was guilty of the offences.
On 20 May 2024, he was sentenced to two 12-month community sentences to run concurrently, disqualified from being a director for five years, and ordered to pay £10,000 towards prosecution costs.
News Story – Legislation / Changes
Managing the risks of workplace transport
Vehicle-related deaths and injuries are preventable if employers take the right steps to assess the risks and implement the right control measures.
In April, an Oldham-based haulage company was fined £86,710 after forklift truck driver Ian Dawson was killed when the HGV he was loading moved forward causing the FLT to overturn, trapping Mr Dawson underneath it. He died as a result of his injuries in 2020.
HSE said the company had failed to put sufficient safe systems of work in place regarding vehicle movements and had not taken steps to ensure all FLT drivers wore seatbelts. The court heard that if Mr Dawson had been wearing a seatbelt it is highly likely that this would have saved his life.
In May, a metals recycling company was fined £1.2m after a worker’s skull was fractured when he was hit by a 32-tonne skip wagon as he walked across the firm’s yard. Neither the man nor the driver saw each other before the collision. The driver had been focusing on manoeuvring his vehicle around some low-level skips which had been placed on a corner near to where the employee was walking.
The court was told the firm had failed to take steps to assess the risks posed by the movement of vehicles and pedestrians at the site.
These are just two tragic examples of what can go wrong when workplace transport risks are not taken seriously. There are many more.
Workplace transport covers any activity involving vehicles used in a workplace. This includes moving goods or people within the workplace; loading, unloading and securing loads; sheeting; coupling; and vehicle maintenance work.
Vehicles using public roads are not usually classed as ‘workplace transport’ because they are covered by road traffic legislation. However, when public roads are used as ‘temporary workplaces’ for example during roadside deliveries, road works or breakdown assistance, health and safety law applies as it does to other workplace transport activities. During these times, employers and drivers have to consider the extra risks their activities may cause to other road users and pedestrians.
On average, each year in Great Britain, HSE says there are around 50 worker deaths and more than 5,000 injuries because of workplace transport activities. The most common causes are people falling from or being struck by a vehicle, objects falling from a vehicle, or vehicles overturning. In the five years from April 2018 to March 2023, 122 workers died after being struck by a moving vehicle at work and over 7,000 sustained non-fatal RIDDOR-reportable injuries.
These deaths and injuries are preventable if employers take the right steps to assess the risks from workplace transport and implement the right control measures.
Causes and measures to take
Most workplace transport-related deaths and injuries are a result of poor segregation of vehicles and pedestrians, inadequate driver training, poor visibility from a vehicle, lack of vehicle maintenance, working on unsafe slopes and surfaces, and poor lighting. To manage these risks effectively, there are three key areas employers need to consider when carrying out a risk assessment:
- Safe site (design and activity) including:
- Planning your workplace so pedestrians are safe from vehicles
- Providing a one-way system if you can
- Providing separate routes for pedestrians and vehicles where possible
- Avoiding reversing where possible
- Providing appropriate crossing points where pedestrians and traffic meet
- Using ‘highway code’ signs to indicate vehicle routes, speed limits, pedestrian crossings etc
- Making sure lighting is adequate where people and vehicles are working
- Keeping road surfaces firm and even
- Making sure there are safe areas for loading and unloading
- Providing separate car parking for visitors as they may not know your site.
- Safe vehicle including:
- Ensuring vehicles are suitable for the purpose for which they are used
- Maintaining vehicles in good repair, particularly the braking system, steering, tyres, lights, mirrors and specific safety systems
- Removing the need for people to climb up on vehicles where possible, e.g. By providing gauges and controls that are accessible from ground level
- Reducing the risk of falling when people have to climb onto a vehicle or trailer by providing well-constructed ladders, non-slip walkways and guard rails where possible
- Providing reversing aids such as cctv where appropriate
- Fitting rollover protective structures and ensuring seatbelts are used where fitted
- Checking that vehicles are inspected daily.
- Safe driver including:
- Checking that drivers are fit to drive
- Ensuring drivers are properly trained
- Ensuring drivers carry out daily vehicle checks
- Ensuring drivers know how to safely enter and exit the vehicle
- Ensuring visiting drivers understand what they have to do to stay safe working on the site.
ICE Risk Management – Product / Services / News
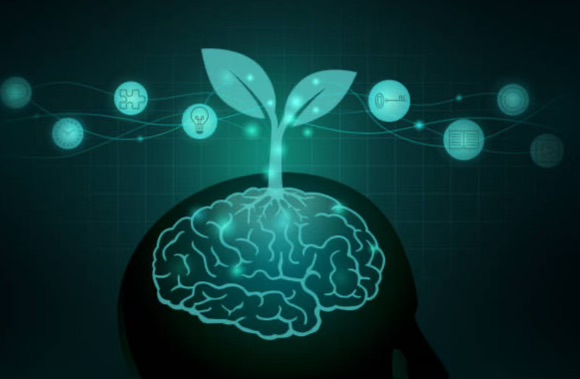
Health and Safety Audits
Regular health and safety audits are key to monitoring the safety standards on your project.
-
Identifying Hazards
A systematic safety audit helps in identifying potential hazards that may be overlooked during daily operations. By conducting routine checks, an extra set of eyes can assist in pinpointing these risks before they lead to accidents or injuries, promoting proactive health & safety rather than reactive.
-
Compliance with Regulations
Construction sites are governed by a range of safety regulations and standards set by local, state, and federal authorities. Safety audits help ensure compliance with these regulations, protecting the company from legal issues, fines, and work stoppages.
-
Promoting a Safety Culture
Regular safety audits reinforce the importance of safety among all workers. They demonstrate a commitment to fostering a safety-first culture where every team member is encouraged to participate in maintaining a safe work environment.
-
Enhancing Worker Morale and Productivity
When workers feel safe and valued, it positively impacts their morale and productivity. Completing safety audits shows that management cares about their well-being, leading to increased job satisfaction and reduced turnover rates.
-
Reducing Costs
Accidents and injuries on construction sites can result in substantial costs, including medical expenses, legal fees, and project delays. By identifying and mitigating risks through safety audits, companies can save money in the long run by preventing costly incidents.
-
Building Reputation
A solid safety record enhances a company’s reputation in the industry. Regular safety audits not only demonstrate a proactive approach to risk management but also build trust with clients, employees & the community.
-
Continuous Improvement
Safety audits are not just about identifying problems; they also provide an opportunity for continuous improvement. By reviewing audit findings, companies can implement changes and best practices that lead to a safer work environment over time.
Conclusion
In summary, completing safety audits is an essential practice that helps protect workers, maintain compliance, and cultivate a positive organisational culture. By prioritising safety on your projects, this does not only ensure the well-being of your employees but also contribute to the overall success and sustainability of your projects. Regular audits are not just a checkbox to mark; they are a vital part of a proactive strategy for safety management in the construction industry.
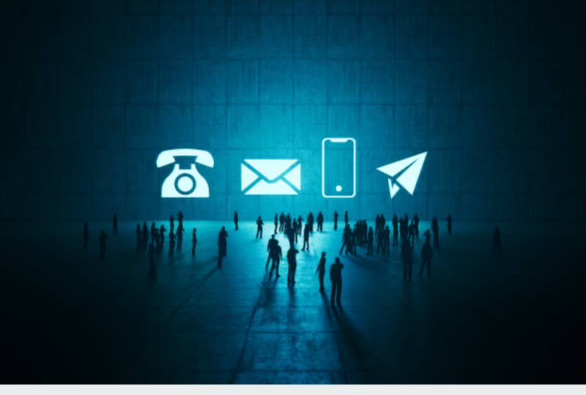